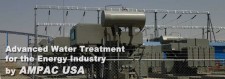
The energy industry has been seeing good results in the past few years and is set to grow in the coming years. The industry needs water to run the day to day operations but the waste they dispose of is now a topic of intense scrutiny. In the past 10-15 years, wastewater disposed by these industries has posed a threat to the environment forcing the emergence of regulations that need to be complied with.
LOS ANGELES, November 29, 2019 (Newswire.com) - The energy industry is growing at a very fast rate and includes both renewable and non-renewable sources. The global energy demand spiked in 2018 by 2.3%. In the U.S., generated electricity in 2014 came from coal, natural gas, nuclear, hydropower, and non-hydro renewables. Water in the energy sector requires equipment for the treatment of its quality, which is why Industrial ROs are used.
Water for the Industry
Water in the energy sector is used to treat boiler makeup water, cooling towers makeup water, and perform condensate polishing for re-use.
The once-through system pulls water directly from natural sources, runs it through the facility, helps the plant generate electricity and is released back. A tower, however, recirculates the water many times through the facility, which may end up evaporating in the process, and as a result, uses 30-70% more water than previous setups.
One of the major sources of industrial water waste is coal plants that run on fossil fuels. “The waste discharge from these plants has significant levels of lead, mercury, and chromium, which are very harmful in concentrated amounts, especially in a mixture,” says Sammy Farag, CEO of AMPAC USA.
Wastewater Treatment
Industrial RO is designed exclusively for two specific purposes in the industry:
- Feedwater treatment involves treating the incoming feed water for chemicals, TDS, suspended solids and any organics that can cause a problem in smooth functioning.
- Wastewater treatment involves treating the water for all intense metal composition that has lead, mercury, arsenic, selenium, and chromium, for regulation compliance.
The features Farag says are most important to the working of such a system are:
- A PLC controller, with all information on the water present. The controller also helps in monitoring various aspects like slow and high-pressure switches, tank levels and pre-treatment equipment.
- Multimedia Carbon Pre-Filters are responsible for chlorine removal, pH adjustment and elimination of excess bacteria. Spin Down Pre-Filter for corrosion resistance and particulate removal. Sediment filter assists in higher flow rates by dirt, sand and sediment removal at high capacity.
- On-demand feed supply pumps supply the system seawater stored in the settling tank in the required pressure and flow. High-pressure plunger pumps are needed to boost pressure up to 1200 psi for better desalination.
Noise reduction, monitors for stainless steel glycerine filled pressure gauges for pressure changes, flow, salinity, temperature, etc., safety features especially being explosion-proof, make it an all-round good system to employ at a power plant.
Source: AMPAC USA
Share: